The Automation Dilemma
- Peter Malek
- May 19, 2016
- 4 min read
What is Continuous Improvement?
CI encompasses the use of multiple proven management and improvement methodologies. There are four methodologies commonly associated with CI:
Lean - Focuses on speed and reducing waste
Six Sigma - Focuses on reducing variation and increasing quality
Theory of Constraints (TOC) - Focuses on identifying and eliminating constraints in a process.
Business Process Re-engineering (BPR) - logical methodology for assessing process weaknesses, identifying gaps, and implementing an enabling technology, solution or system to streamline and improve processes.
The primary objectives of CI include but are not limited to:
Increasing speed of decisions, transactions, paperwork, etc.
Enhancing quality of outputs
Improving customer satisfaction
Increasing and enhancing the quality of work life
Reducing overhead costs
Increasing safety
What is Business Process Re-Engineering?

Redesign of business processes to achieve dramatic improvements in critical, contemporary measures of performance, such as cost, quality, service and speed by way primarily of a material solution (IT/Automation) change or improvement.
What is Lean Six Sigma?

Lean is embodied by five key principles:
Value has been specified from the Customer’s perspective
The Value Stream has been identified for each product/service
The product/service Flows without interruptions
The Customer can Pull value from the process
Continuous pursuit of Perfection
“Six Sigma” is an optimized performance level approaching zero defects in any process, whether it produces a:
Product
Service
Transaction
A Six Sigma process results in only 3.4 defects per million opportunities (DPMO).
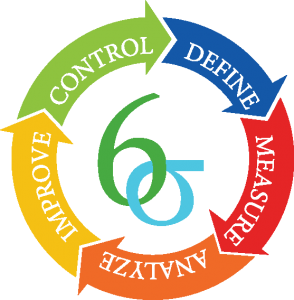
When implementing Lean Six Sigma, a Define, Measure, Analyze, Improve and Control (DMAIC) ordered problem-solving methodology/framework is applied. The letters are an acronym for the five phases of a Lean Six Sigma improvement and widely used across public and private sector. These phases direct a continuous improvement team logically from problem definition to implementing solutions that are linked to root causes. The methodology also focuses on establishing best practices to help ensure the improvement solutions stay in place.
DMAIC is typically implemented through two primary modes in Six Sigma improvement efforts, the traditional DMAIC project team approach–which normally involves full time deployment of key team members for 3 to 6 months or the kaizen or Rapid Improvement Event (RIE) approach–which stresses rapid, intense progress through all DMAIC stages except full-scale implementation. The DMAIC phases and problem-solving construct is the primary foundation of all Continuous Improvement related projects, and a way of thinking that help guide a standardized, structured, and data-driven approach to achieve and measure results.
What is Process Robotics/Automation?

As defined by Gartner, Robotic automation provides a way of reducing operating costs while also facilitating agility as the organization responds to customers’ evolving needs. Robotic automation involves the provision of software tooling that enables organizations to automate existing user actions — as if the user were moving through and across their current raft of applications.
"Busting" the Process Automation Myth
Process robotics is a technology solution layer that further enables/enhances the deployment of Continuous Improvement. When you are coming out of the Analysis phase of DMAIC and targeting to make future state improvements based on the data that you have collected, having knowledge of technology solutions and the ability to potentially offer this as a future state improvement for process activities that are relevant, provides the customer with one of many potential accelerators to efficiently and effectively target cost savings.
Furthermore, Continuous Improvement methodologies and tools help establish the foundation for building the case around the need and cost/benefit of implementing process robotics/automation solutions. The data collection and process mapping involved with defining a current state and establishing a current state baseline provides organizations with data driven root cause analysis of time, transaction volume, costs, and errors that are candidates and would potentially benefit the most from automation as part of a future state solution.
Process Robotics according to industry research and studies is considered an alternative to conducing Business Process Re-engineering and more of a disruptive technology solution that might be trying to compete with replacing or modernizing systems that can now be automated without re-engineering the steps and going through the time and resource costs often associated with requirements definition, design, testing, and implementation of a new solution when you can simply automate existing steps removing the human-in-the-loop. Forrester's report on Building a Center of Expertise to support Robotic Automation highlights the following five key paradigm shifts between process robotics/automation and business process re-engineering:
Focuses on replacement of FTE's with a virtual worker to enable the long tail of change and cost reduction vs. re-engineering the underlying process to drive efficiency
Automates existing processes versus creating a new application
Automates repetitive tasks reusing applications, interfaces, and web services versus data being passed between new application and back-end systems
Robotic automation has the same capability of humans requiring no testing versus extensive testing interfaces between applications and associated data layer integration
Enables IT, business analysts and Admins to self-serve versus configuration and complex development of user interface
It is also important to note that process robotics/automation implies developing skills in business and IT domains. In order to properly implement a process robotics/automation solution according to leading research firms, a critical part of the core business team established to make these automation solutions a reality, requires a Continuous Improvement background and set of skills such as Lean Six Sigma.

The art of being a successful Lean Six Sigma expert and process improvement practitioner is continuously improving your knowledge of various tools and techniques, your ability to adapt and tailor methods, and your ability to apply the tools and techniques to optimize business results/outcomes for any given problem, while improving the experience for both the internal and external customers alike.
So if someone tells you that traditional Continuous Improvement and Lean Six Sigma is a thing of the past, and process robotics/automation is the future, just remember to challenge them with how they will identify the need for process robotics/automation without first applying a disciplined continuous improvement approach to Define, Measure, and Analyze the problem they are trying to Improve and Control through automation. Bottom line - continuous improvement and business process optimization is on the critical path to identifying opportunities and building the case for process robotics/automation.

As always, please share your views and let me know what your thoughts are. Does this make sense? Do you agree or not?
Comments